1. Was ist Plasma?
Plasma ist ein vierter Aggregatzustand, ein ionisiertes Gas, das auf eine extrem hohe Temperatur erhitzt und ionisiert wurde, so dass es elektrisch leitfähig wird. Beim Plasmaschneiden und -fugenhobeln wird dieses Plasma verwendet, um einen elektrischen Lichtbogen auf das Werkstück zu übertragen. Das zu schneidende oder zu entfernende Metall wird durch die Hitze des Lichtbogens geschmolzen und dann weggeblasen. Während das Ziel des Plasmaschneidens das Trennen des Materials ist, wird das Fugenhobeln dazu verwendet, Metalle in einer kontrollierten Tiefe und Breite zu entfernen.
Plasmabrenner sind ähnlich aufgebaut wie die Zündkerze eines Autos. Sie bestehen aus einem negativen und einem positiven Teil, die durch einen mittleren Isolator getrennt sind. Im Inneren des Brenners wird der Pilotlichtbogen in der Lücke zwischen der negativ geladenen Elektrode und der positiv geladenen Spitze gezündet. Sobald der Pilotlichtbogen das Plasmagas ionisiert hat, strömt die überhitzte Gassäule durch die kleine Öffnung in der Brennerspitze, die auf das zu schneidende Metall gerichtet ist.
In einem Plasmaschneidbrenner tritt ein kühles Gas in Zone B ein, wo ein Pilotlichtbogen zwischen der Elektrode und der Brennerspitze das Gas erhitzt und ionisiert. Der Hauptschneidlichtbogen wird dann durch die Plasmagassäule in Zone C auf das Werkstück übertragen. Indem das Plasmagas und der Lichtbogen durch eine kleine Öffnung gepresst werden, liefert der Brenner eine hohe Wärmekonzentration auf einer kleinen Fläche. Der steife, eingeschnürte Plasmalichtbogen ist in Zone C zu sehen. Beim Plasmaschneiden wird Gleichstrom (DC) mit gerader Polarität verwendet, wie in der Abbildung dargestellt. Zone A leitet ein Sekundärgas, das den Brenner kühlt. Dieses Gas unterstützt auch das Hochgeschwindigkeitsplasmagas beim Herausblasen des geschmolzenen Metalls aus dem Schnitt, wodurch ein schneller, schlackenfreier Schnitt ermöglicht wird.
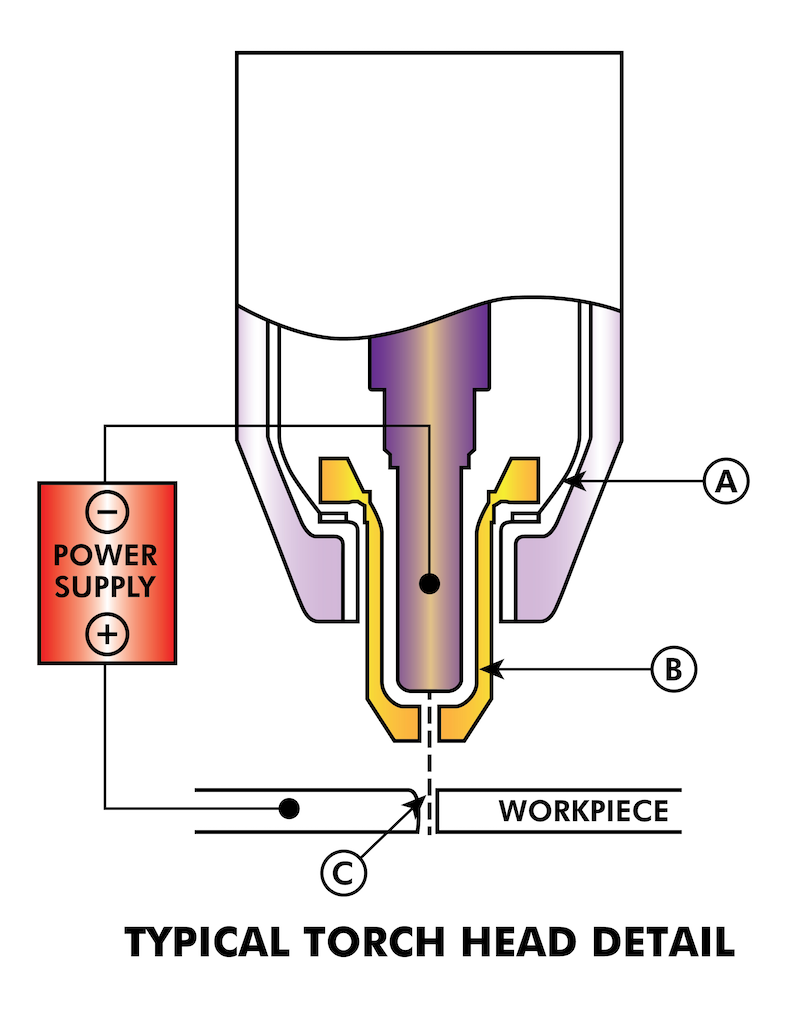
2. Bogen-Initialisierung
Es gibt zwei Hauptmethoden für die Lichtbogeninitialisierung bei Plasmaschneidanlagen, die für den CNC-Betrieb ausgelegt sind. Während andere Methoden auf einigen Maschinen verwendet werden (z. B. Scratch-Start, wo physischer Kontakt mit dem Material erforderlich ist), sind sie für CNC-Anwendungen ungeeignet…
2.1. Hochfrequenzstart
Dieser Starttyp ist weit verbreitet und am längsten im Einsatz. Obwohl es sich um eine ältere Technologie handelt, funktioniert sie gut und startet schnell. Aufgrund der Hochfrequenz-Hochspannung, die zur Ionisierung der Luft erforderlich ist, hat sie jedoch einige Nachteile. Sie stört oft die umliegenden elektronischen Schaltkreise und kann sogar Bauteile beschädigen. Außerdem ist ein spezieller Schaltkreis erforderlich, um einen Pilotbogen zu erzeugen. Preiswerte Modelle verfügen nicht über einen Pilotlichtbogen und erfordern eine Berührung des Verbrauchsmaterials mit dem Werkstück, um es zu starten. Die Verwendung eines HF-Schaltkreises kann auch den Wartungsaufwand erhöhen, da es in der Regel einstellbare Punkte gibt, die von Zeit zu Zeit gereinigt und neu eingestellt werden müssen.
2.2. Blowback Start
Bei diesem Starttyp wird ein kleiner Kolben oder eine Kartusche im Brennerkopf durch den Luftdruck, der dem Schneidgerät zugeführt wird, zurückgedrückt, um einen kleinen Funken zwischen der Innenfläche des Verschleißteils zu erzeugen, der die Luft ionisiert und eine kleine Plasmaflamme erzeugt. Dadurch wird auch ein "Pilotlichtbogen" erzeugt, der für eine Plasmaflamme sorgt, die brennt, egal ob sie mit dem Metall in Kontakt ist oder nicht. Dies ist ein sehr guter Starttyp, der inzwischen von mehreren Herstellern verwendet wird. Ihr Vorteil ist, dass sie etwas weniger Schaltkreise benötigt, recht zuverlässig ist und weitaus weniger elektrisches Rauschen erzeugt.
Bei CNC-Luftplasmasystemen der Einstiegsklasse wird der Blowback-Stil bevorzugt, um elektrische Interferenzen mit der Elektronik und Standard-PCs zu minimieren, aber bei größeren Maschinen ab 200 Ampère ist der Hochfrequenzstart immer noch die Regel. Diese erfordern PCs und Elektronik auf Industrieniveau, und selbst kommerzielle Hersteller hatten Probleme mit Fehlern, weil sie es versäumt haben, das elektrische Rauschen in ihren Konstruktionen zu berücksichtigen.
3. CNC-Plasma
Die Plasmabearbeitung auf CNC-Maschinen ist im Vergleich zum Fräsen oder Drehen ziemlich einzigartig und ein etwas verwaistes Verfahren. Eine ungleichmäßige Erwärmung des Materials durch den Plasmalichtbogen führt dazu, dass sich das Blech biegt und verzieht. Die meisten Bleche kommen nicht in einem sehr gleichmäßigen oder flachen Zustand aus dem Walzwerk oder der Presse. Dicke Bleche (30 mm und mehr) können um 50 mm bis 100 mm aus der Ebene geraten. Die meisten anderen CNC-G-Code-Operationen beginnen mit einer bekannten Referenz oder einem Stück Material, das eine bekannte Größe und Form hat, und der G-Code wird geschrieben, um den Überschuss abzuschruppen und dann das fertige Teil zu schneiden. Bei Plasma ist es aufgrund des unbekannten Zustands des Blechs unmöglich, einen G-Code zu erstellen, der diese Abweichungen im Material berücksichtigt.
Ein Plasmalichtbogen hat eine ovale Form, und die Schnitthöhe muss kontrolliert werden, um abgeschrägte Kanten zu minimieren. Wenn der Brenner zu hoch oder zu niedrig ist, können die Kanten übermäßig abgeschrägt werden. Es ist auch wichtig, dass der Brenner senkrecht zur Oberfläche gehalten wird.
-
Torch to work distance can impact edge bevel
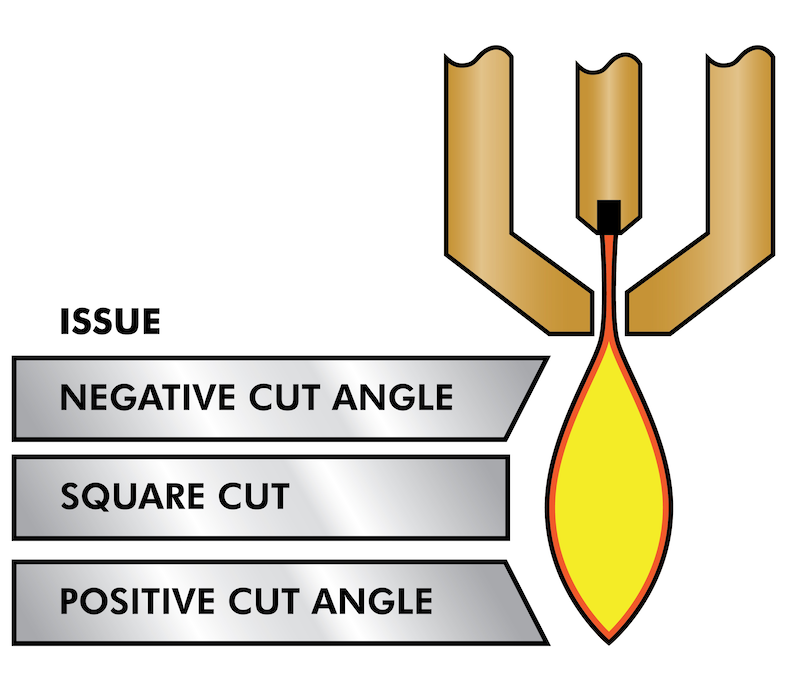
-
Negative cut angle: torch too low, increase torch to work distance.
-
Positive cut angle: torch too high, decrease torch to work distance.
Anmerkung
|
Eine leichte Abweichung der Schnittwinkel kann normal sein, solange sie innerhalb der Toleranz liegt. |
Die Fähigkeit, die Schnitthöhe in einer solch feindlichen und sich ständig verändernden Umgebung präzise zu steuern, ist eine sehr schwierige Herausforderung. Glücklicherweise gibt es eine sehr lineare Beziehung zwischen der Brennerhöhe (Lichtbogenlänge) und der Lichtbogenspannung, wie diese Grafik zeigt.
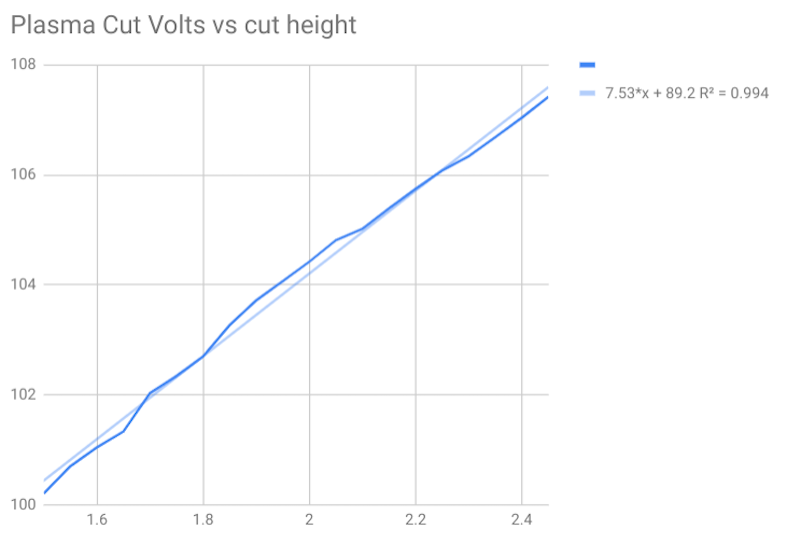
Dieses Diagramm wurde aus einer Stichprobe von etwa 16.000 Messwerten bei unterschiedlichen Schnitthöhen erstellt, und die Regressionsanalyse zeigt 7,53 V/mm mit einer Zuverlässigkeit von 99,4 %. In diesem speziellen Fall wurde die Stichprobe von einer Everlast-Maschine mit 50 A entnommen, die von LinuxCNC gesteuert wird.
Die Brennerspannung ist dann eine ideale Prozesssteuerungsvariable für die Einstellung der Schnitthöhe. Nehmen wir der Einfachheit halber an, dass sich die Spannung um 10 V/mm ändert. Dies kann umgerechnet werden als 1 Volt pro 0,1 mm (0,004"). Die großen Plasmamaschinenhersteller (z. B. Hypertherm, Thermal Dynamics und ESAB) geben Schneidtabellen heraus, in denen die empfohlene Schneidhöhe und die geschätzte Lichtbogenspannung bei dieser Höhe sowie einige zusätzliche Daten angegeben sind. Wenn also die Lichtbogenspannung 1 V höher ist als die Herstellerangaben, muss die Steuerung den Brenner lediglich um 0,1 mm (0,004") absenken, um die gewünschte Schneidhöhe zu erreichen. Zur Steuerung dieses Prozesses wird üblicherweise eine Brennerhöhensteuerung (THC) verwendet.
4. Auswahl einer Plasmamaschine für CNC-Bearbeitungen
Auf dem Markt gibt es heute eine Vielzahl von Plasmamaschinen, von denen nicht alle für den CNC-Einsatz geeignet sind. CNC-Plasmaschneiden ist ein komplexer Vorgang, und es wird empfohlen, dass Integratoren eine geeignete Plasmamaschine auswählen. Andernfalls kann es zu stundenlanger, erfolgloser Fehlersuche kommen, wenn man versucht, das Fehlen von Funktionen zu umgehen, die viele als obligatorisch ansehen würden.
Obwohl Regeln dazu da sind, gebrochen zu werden, wenn man die Gründe für die Anwendung der Regel versteht, sind wir der Meinung, dass ein neuer Hersteller von Plasmatischen eine Maschine mit den folgenden Merkmalen auswählen sollte:
-
Blowback-Start zur Minimierung der elektrischen Geräusche und zur Vereinfachung der Konstruktion
-
Ein Maschinenbrenner wird bevorzugt, aber viele haben auch Handbrenner verwendet.
-
Eine vollständig abgeschirmte Brennerspitze, die eine ohmsche Abtastung ermöglicht
Wenn Sie über das nötige Budget verfügen, können Sie sich für ein höherwertiges Gerät entscheiden:
-
Vom Hersteller bereitgestellte Schneidtabellen, die viele Stunden und Materialabfälle bei der Kalibrierung der Schneidparameter sparen
-
Potentialfreie Kontakte für ArcOK
-
Klemmen für Lichtbogen-Ein (engl. Arc On)-Schalter
-
Ausgang für rohe Lichtbogenspannung (engl. raw arc voltage) oder geteilte Lichtbogenspannung
-
Optional eine RS485-Schnittstelle, wenn Sie einen Hypertherm-Plasma-Cutter verwenden und diesen von der LinuxCNC-Konsole aus steuern möchten.
-
Höhere Einschaltzyklen
In jüngster Zeit ist eine andere Maschinenklasse, die einige dieser Funktionen enthält, für rund 550 US-Dollar erhältlich geworden. Ein Beispiel ist der Herocut55i, der bei Amazon erhältlich ist, aber es gibt noch kein Feedback von Benutzern. Diese Maschine verfügt über einen Blasbrenner, ArcOK-Ausgang, Brennerstartkontakte und rohe Lichtbogenspannung.
5. Arten der Brennerhöhensteuerung
Die meisten THC-Einheiten sind externe Geräte und viele haben eine ziemlich grobe "Bit Bang" -Anpassungsmethode. Sie liefern zwei Signale zurück an die LinuxCNC-Steuerung. Einer schaltet sich ein, wenn sich die Z-Achse nach oben bewegen soll, und der andere schaltet sich ein, wenn sich die Z-Achse nach unten bewegen soll. Keines der beiden Signale ist wahr, wenn sich die Taschenlampe auf der richtigen Höhe befindet. Das beliebte Proma 150 THC ist ein Beispiel für diese Art von THC. Die LinuxCNC THCUD-Komponente wurde entwickelt, um mit dieser Art von THC zu arbeiten.
Mit der Veröffentlichung der Mesa THCAD Spannung zu Frequenz-Schnittstelle, war LinuxCNC in der Lage, die tatsächliche Brennerspannung über einen Encoder-Eingang zu decodieren. Dies ermöglichte LinuxCNC, um die Z-Achse zu steuern und zu beseitigen externe Hardware. Frühe Implementierungen unter Verwendung der THCAD repliziert die "Bit-Bang"-Ansatz. Die LinuxCNC THC Komponente ist ein Beispiel für diesen Ansatz.
Jim Colt von Hypertherm hat zu Protokoll gegeben, dass die besten THC-Controller vollständig in die CNC-Steuerung selbst integriert wurden. Natürlich bezog er sich auf High-End-Systeme, die von Hypertherm, Esab, Thermal Dynamics und anderen wie Advanced Robotic Technology in Australien hergestellt wurden, und träumte nicht davon, dass Open Source mit diesem Ansatz Systeme produzieren könnte, die mit High-End-Systemen konkurrieren.
Die Einbeziehung externer Offsets in Linuxcnc V2.8 ermöglichte es der Plasmasteuerung in LinuxCNC, auf ein ganz neues Niveau zu steigen. Externe Offsets beziehen sich auf die Möglichkeit, einen Versatz auf die Achsenbefehlsposition außerhalb des Motion Controllers anzuwenden. Dies ist perfekt für die Plasma-THC-Kontrolle als Methode zur Anpassung der Brennerhöhe in Echtzeit basierend auf unserer gewählten Prozesssteuerungsmethodik. Nach einer Reihe von experimentellen Builds wurde die Plasmac-Konfiguration in LinuxCNC 2.8 integriert. QtPlasmaC hat Plasmac in LinuxCNC 2.9 abgelöst. Dies war ein äußerst ehrgeiziges Projekt und viele Menschen auf der ganzen Welt waren am Testen und Verbessern des Funktionsumfangs beteiligt. QtPlasmaC ist insofern einzigartig, als sein Designziel darin bestand, alle THCs zu unterstützen, einschließlich der einfachen Bit-Bang-THCs bis hin zur ausgeklügelten Brennerspannungssteuerung, wenn die Spannung LinuxCNC über einen THCAD oder einen anderen Spannungssensor zur Verfügung gestellt wird. Darüber hinaus ist QtPlasmaC als eigenständiges System konzipiert, das keine zusätzlichen G-Code-Subroutinen benötigt und es dem Benutzer ermöglicht, eigene Schnittdiagramme zu definieren, die im System gespeichert sind und über ein Dropdown-Menü zugänglich sind.
6. Lichtbogen-OK-Signal
Plasmageräte mit einer CNC-Schnittstelle enthalten eine Reihe von Trockenkontakten (z. B. ein Relais), die sich schließen, wenn ein verlässlicher Lichtbogen entsteht, und jede Seite dieser Kontakte ist mit Stiften an der CNC-Schnittstelle verbunden. Der Erbauer eines Plasmatisches sollte eine Seite dieser Stifte mit der Feldspannung und die andere mit einem Eingangsstift verbinden. Auf diese Weise kann die CNC-Steuerung erkennen, wann ein gültiger Lichtbogen entstanden ist und wann er unerwartet verloren geht. Hier gibt es eine potenzielle Falle, wenn es sich bei dem Eingang um eine Schaltung mit hoher Impedanz handelt, wie z. B. eine Mesa-Karte. Handelt es sich bei den potentialfreien Kontakten um ein einfaches Relais, ist die Wahrscheinlichkeit groß, dass der durch das Relais fließende Strom unter der Mindeststromspezifikation liegt. Unter diesen Bedingungen kann es bei den Relaiskontakten zu einer Oxidbildung kommen, die mit der Zeit zu einem intermittierenden Betrieb der Kontakte führen kann. Um dies zu verhindern, sollte ein Pull-Down-Widerstand am Eingangsstift des Reglers installiert werden. Es sollte darauf geachtet werden, dass dieser Widerstand so gewählt wird, dass der Mindeststrom durch das Relais fließt und er eine ausreichende Wattzahl hat, um die Leistung im Schaltkreis zu bewältigen. Schließlich sollte der Widerstand so montiert werden, dass die entstehende Wärme während des Betriebs keine Schäden verursacht.
Wenn Sie ein ArcOK-Signal haben, wird empfohlen, es über jedes synthetisierte Signal hinaus zu verwenden, um potenzielle Build-Probleme zu beseitigen. Ein synthetisiertes Signal, das von einem externen THC- oder QtPlasmaC-Modus 0 verfügbar ist, kann die ArcOK-Schaltung in einem Plasmawechselrichter nicht vollständig ersetzen. Einige Build-Probleme wurden beobachtet, bei denen eine Fehlkonfiguration oder Inkompatibilität mit dem Plasma-Wechselrichter durch ein synthetisiertes ArcOK-Signal aufgetreten ist. Im Großen und Ganzen ist jedoch ein korrekt konfiguriertes synthetisiertes ArcOK-Signal in Ordnung.
Ein einfaches und effektives ArcOK-Signal kann mit einem einfachen Reedrelais erreicht werden. Wickeln Sie 3 Umdrehungen eines der dicken Kabel des Plasma-Cutters drarum, z. B. das Materialklemmkabel. Setzen Sie das Relais zum Schutz in ein altes Stiftrohr ein und schließen Sie eine Seite des Relais an die Feldstromversorgung und das andere Ende an den ArcOK-Eingangspin an.
7. Erfassung der Anfangshöhe
Da die Schnitthöhe ein so kritischer Systemparameter ist und die Materialoberfläche von Natur aus uneben ist, benötigt ein Z-Achsen-Mechanismus eine Methode, um die Materialoberfläche zu erfassen. Es gibt drei Methoden, um dies zu erreichen:
-
Stromabtastung zur Erkennung eines erhöhten Motordrehmoments,
-
ein "Schwimmer"-Schalter und ein elektrischer oder
-
Ein "ohmscher" Messkreis, der geschlossen wird, wenn der Brennerschild das Material berührt.
Strommessung ist keine praktikable Technik für DIY-Tabellen, aber Schwimmerschalter und ohmsche Messung werden weiter unten besprochen:
7.1. Gleitende Schalter (engl. float switches)
Der Brenner ist auf einem Gleittisch montiert, der sich nach oben bewegen kann, wenn die Brennerspitze die Materialoberfläche berührt und einen Schalter oder Sensor auslöst. Oft wird dies unter G-Code-Steuerung mit den G38-Befehlen erreicht. Wenn dies der Fall ist, wird empfohlen, nach der ersten Sondierung von der Oberfläche wegzutasten, bis das Sondensignal mit einer langsameren Geschwindigkeit verloren geht. Stellen Sie außerdem sicher, dass die Schalterhysterese berücksichtigt wird.
Unabhängig von der verwendeten Sondierungsmethode wird dringend empfohlen, einen gleitenden Schalter einzubauen, damit ein Ausweich- oder Sekundärsignal vorhanden ist, um eine Beschädigung des Brenners bei einem Absturz zu vermeiden.
7.2. Ohmsche Erfassung
Die ohmsche Abtastung beruht auf dem Kontakt zwischen dem Brenner und dem Material, der wie ein Schalter wirkt, um ein elektrisches Signal zu aktivieren, das von der CNC-Steuerung erfasst wird. Unter der Voraussetzung, dass das Material sauber ist, kann dies eine viel genauere Methode zur Abtastung des Materials sein als ein Schwimmerschalter, der eine Ablenkung der Materialoberfläche verursachen kann. Dieser ohmsche Abtastkreis arbeitet in einer extrem feindlichen Umgebung, so dass eine Reihe von Ausfallsicherungen implementiert werden müssen, um die Sicherheit sowohl der CNC-Elektronik als auch des Bedieners zu gewährleisten. Beim Plasmaschneiden ist die am Material befestigte Erdungsklemme positiv und der Brenner ist negativ. Es wird empfohlen, dass:
-
Die ohmsche Abtastung kann nur dann eingesetzt werden, wenn der Brenner eine Abschirmung hat, die von der Brennerspitze isoliert ist, die den Schneidlichtbogen leitet.
-
Der ohmsche Schaltkreis verwendet eine völlig getrennte, isolierte Stromversorgung, die ein optoisoliertes Relais aktiviert, damit das Abtastsignal an die CNC-Steuerung übertragen werden kann.
-
Die positive Seite des Stromkreises sollte am Brenner liegen.
-
Beide Seiten des Stromkreises müssen durch optoisolierte Relais isoliert werden, bis die Messung durchgeführt wird.
-
Es müssen Sperrdioden verwendet werden, um zu verhindern, dass Lichtbogenspannung in den ohmschen Messkreis gelangt.
Im Folgenden finden Sie eine Beispielschaltung, die sich bewährt hat und mit der LinuxCNC QtPlasmaC-Konfiguration kompatibel ist.
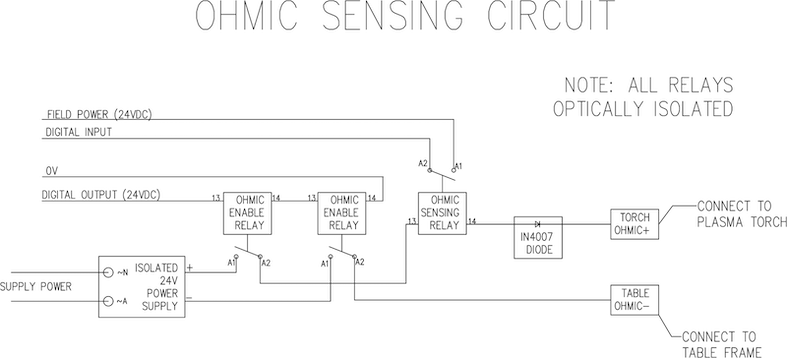
7.3. Hypersensing mit einem MESA THCAD-5
Eine ausgefeiltere Methode der Materialerkennung, bei der die Relais und Dioden entfallen, ist die Verwendung eines weiteren THCAD-5 zur Überwachung der Spannung des Materialerkennungsschaltkreises über eine isolierte Stromversorgung. Dies hat den Vorteil, dass das THCAD für die feindliche elektrische Umgebung des Plasmas ausgelegt ist und die Logikseite vollständig und sicher von der Hochspannungsseite isoliert.
Um diese Methode zu implementieren, ist ein zweiter Encodereingang erforderlich.
Bei Verwendung einer Mesa-Karte ist eine andere Firmware verfügbar, die 2 zusätzliche Encoder A-Eingänge an den Pins Encoder B und Encoder Index bereitstellt. Diese Firmware kann für die Karten 7I76E und 7I96 von der Mesa-Website auf den Produktseiten heruntergeladen werden.
Der THCAD ist empfindlich genug, um den Anstieg der Schaltungsspannung bei steigendem Kontaktdruck zu erkennen. Die in LinuxCNC enthaltene Komponente ohmic.comp kann die Abtastspannung überwachen und einen Spannungsschwellenwert festlegen, bei dessen Überschreitung davon ausgegangen wird, dass ein Kontakt hergestellt und ein Ausgang aktiviert ist. Durch die Überwachung der Spannung kann ein niedrigerer Schwellenwert für die Unterbrechung des Stromkreises festgelegt werden, um eine starke Schalterhysterese einzubauen. Dadurch werden Fehlauslösungen minimiert. In unseren Tests haben wir festgestellt, dass die Materialerfassung mit dieser Methode empfindlicher und robuster ist und die Verdrahtung einfacher zu realisieren ist. Ein weiterer Vorteil der Verwendung von Softwareausgängen anstelle von physischen E/A-Pins ist, dass dadurch Pins für andere Zwecke frei werden. Dieser Vorteil ist hilfreich, um das Beste aus dem Mesa 7I96 herauszuholen, das über begrenzte E/A-Pins verfügt.
Der folgende Schaltplan zeigt, wie eine Hypersensing-Schaltung realisiert werden kann.
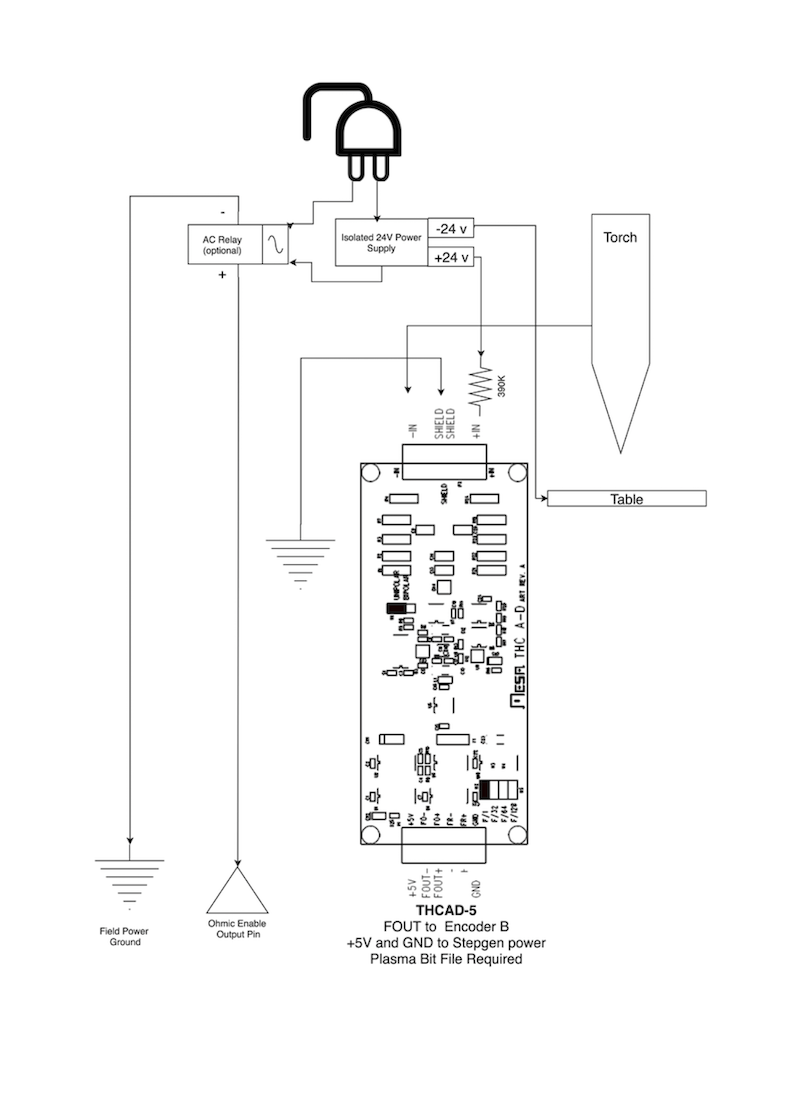
Wir haben eine 15 W Mean Well HDR-15 Ultra Slim DIN Rail Supply 24 V DIN-Schienen-basierte isolierte Stromversorgung verwendet. Dies ist ein doppelt isoliertes Gerät der Isolationsklasse II, das jeder Lichtbogenspannung standhält, die an die Klemmen angelegt werden könnte.
7.4. Beispiel HAL-Code für Hypersensing
Der folgende HAL-Code kann in die custom.hal von QtPlasmaC eingefügt werden, um die ohmsche Abtastung am Encoder 2 einer 7I76E zu aktivieren. Installieren Sie die richtige Bit-Datei und schließen Sie den THCAD an IDX+ und IDX- an. Stellen Sie sicher, dass die Kalibrierungseinstellungen mit denen Ihres THCAD-5 übereinstimmen.
# --- Load the Component --- loadrt ohmic names=ohmicsense addf ohmicsense servo-thread # --- 7I76E ENCODER 2 SETUP FOR OHMIC SENSING--- setp hm2_7i76e.0.encoder.02.scale -1 setp hm2_7i76e.0.encoder.02.counter-mode 1 # --- Configure the component --- setp ohmicsense.thcad-0-volt-freq 140200 setp ohmicsense.thcad-max-volt-freq 988300 setp ohmicsense.thcad-divide 32 setp ohmicsense.thcad-fullscale 5 setp ohmicsense.volt-divider 4.9 setp ohmicsense.ohmic-threshold 22.0 setp ohmicsense.ohmic-low 1.0 net ohmic-vel ohmicsense.velocity-in <= hm2_7i76e.0.encoder.02.velocity # --- Replace QtPlasmaC's Ohmic sensing signal --- unlinkp db_ohmic.in net ohmic-true ohmicsense.ohmic-on => db_ohmic.in net plasmac:ohmic-enable => ohmicsense.is-probing
8. THC-Verzögerung
Wenn ein Lichtbogen entsteht, steigt die Lichtbogenspannung deutlich an und pendelt sich dann wieder auf eine stabile Spannung auf Höhe des Schnittes ein. Wie die grüne Linie in der Abbildung unten zeigt.
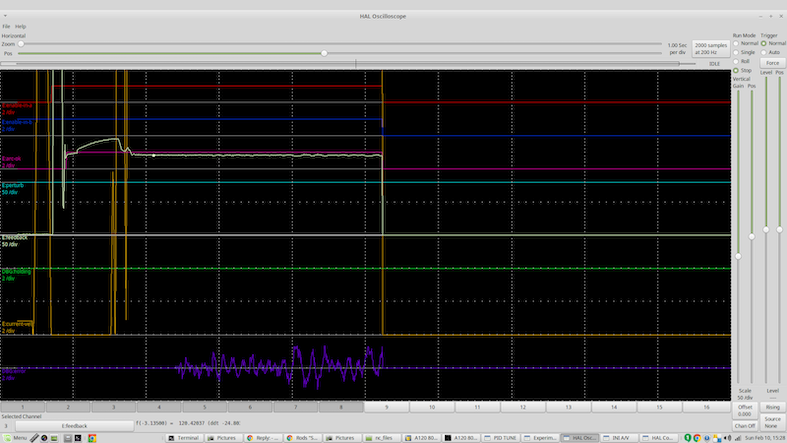
Es ist wichtig, dass die Plasmasteuerung "abwartet", bevor sie die Brennerspannung automatisch abtastet und mit der THC-Regelung beginnt. Wenn sie zu früh aktiviert wird, liegt die Spannung über der gewünschten Abschaltspannung und der Brenner wird heruntergefahren, um einen vermeintlichen Überhöhungszustand zu beheben.
In unseren Tests variiert dies je nach Maschine und Material zwischen 0,5 und 1,5 s. Daher ist eine Verzögerung von 1,5 Sekunden nach einem gültigen arcOK Signal empfangen wird, bevor die THC-Steuerung ist eine sichere Grundeinstellung. Wenn Sie dies für ein bestimmtes Material zu verkürzen wollen, wird LinuxCNC Halscope können Sie die Brennerspannung zu plotten und fundierte Entscheidungen über die kürzeste sichere Verzögerung verwendet wird.
Anmerkung
|
Liegt die Schnittgeschwindigkeit am Ende dieser Verzögerung noch nicht in der Nähe der gewünschten Schnittgeschwindigkeit, sollte die Steuerung warten, bis diese erreicht ist, bevor sie die THC aktiviert. |
9. Abtastung der Brennerspannung
Anstatt sich auf die Schneidtabellen des Herstellers zu verlassen, um die gewünschte Brennerspannung einzustellen, ziehen es viele Leute (einschließlich des Verfassers) vor, die Spannung zu messen, wenn die THC aktiviert ist, und diese als Sollwert zu verwenden.
10. Brenner Behinderung (engl. torch breakaway)
Es wird empfohlen, einen Mechanismus vorzusehen, der es dem Brenner ermöglicht, im Falle eines Aufpralls auf das Material oder eines hochgekippten Schneidteils "abzukommen" oder abzufallen. Es sollte ein Sensor installiert werden, damit die CNC-Steuerung erkennen kann, ob dies geschehen ist, und das laufende Programm anhalten kann. Normalerweise wird eine Abreißsicherung mit Magneten realisiert, um den Brenner am Z-Achsentisch zu befestigen.
11. Eckensicherung (engl. corner lock) / Verhindern von Eintauchen bei Geschwindigkeitsänderung (engl. velocity anti-dive)
Die LinuxCNC Trajektorie Planer ist verantwortlich für die Übersetzung Geschwindigkeit und Beschleunigung Befehle in Bewegung, die den Gesetzen der Physik gehorchen. Zum Beispiel wird die Bewegung zu verlangsamen, wenn die Verhandlung einer Ecke. Während dies bei Fräsmaschinen oder Oberfräsen kein Problem ist, stellt dies beim Plasmaschneiden ein besonderes Problem dar, da die Lichtbogenspannung bei langsamerer Bewegung steigt. Dies führt dazu, dass die THC den Brenner herunterfährt. Einer der enormen Vorteile einer THC-Steuerung innerhalb der LinuxCNC Motion Controller eingebettet ist, dass es weiß, was los ist zu allen Zeiten. So wird es eine triviale Angelegenheit, um die aktuelle Geschwindigkeit (motion.current-velocity
) zu überwachen und THC-Betrieb zu halten, wenn es unter einen bestimmten Schwellenwert fällt (zB 10% unter dem gewünschten Vorschub).
12. Hohlraum- / Schnitt-Kreuzung (engl. void/kerf crossing)
Wenn der Plasmabrenner beim Schneiden über einen Hohlraum fährt, steigt die Lichtbogenspannung schnell an und die THC reagiert mit einer heftigen Abwärtsbewegung, die den Brenner in das Material schlagen und es möglicherweise beschädigen kann. Dies ist eine Situation, die schwer zu erkennen und zu handhaben ist. Bis zu einem gewissen Grad kann dies durch gute Verschachtelungstechniken gemildert werden, aber bei dickerem Material kann es immer noch vorkommen, dass etwas Schlacke herausfällt. Dies ist das eine Problem, das noch innerhalb der LinuxCNC Open-Source-Bewegung gelöst werden muss.
Ein vorgeschlagenes Verfahren ist die Überwachung der Änderungsrate der Brennerspannung über die Zeit (dv/dt), da dieser Parameter beim Durchqueren eines Hohlraums um Größenordnungen höher ist als bei normaler Verformung des Materials. Das folgende Diagramm zeigt eine niedrig aufgelöste Darstellung von dv/dt (in blau) beim Durchqueren eines Hohlraums. Die rote Kurve ist ein gleitender Durchschnitt der Brennerspannung.
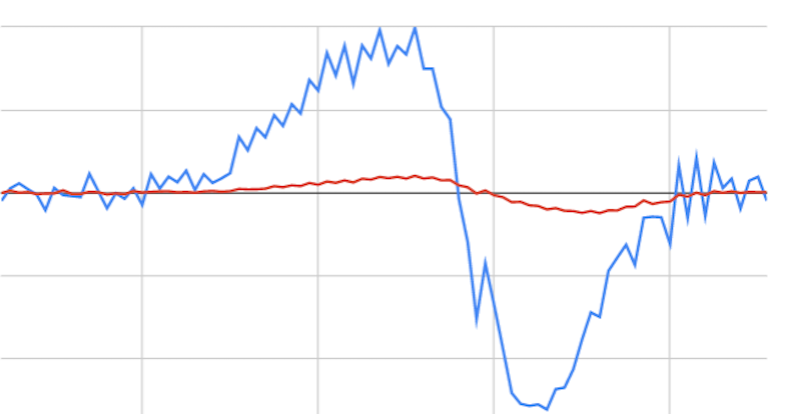
So sollte es möglich sein, den gleitenden Durchschnitt mit dem dv/dt zu vergleichen und THC-Betrieb zu stoppen, sobald die dv/dt den normalen Bereich aufgrund von Verzug erwartet überschreitet. Es muss noch mehr Arbeit in diesem Bereich investiert werden, damit es zu einer funktionierenden Lösung in LinuxCNC kommt.
13. Schneiden von Löchern und kleinen Formen
Beim Schneiden von Löchern und kleinen Formen empfiehlt es sich, den Schnitt zu verlangsamen.
John Moore sagt: "Wenn Sie Einzelheiten über das Schneiden von präzisen kleinen Löchern erfahren möchten, sehen Sie sich die Verkaufsunterlagen über die True Hole Technology von Hypertherm an, und schauen Sie auch auf PlasmaSpider nach, der Benutzer seanp hat ausführlich über seine Arbeit mit einfachem Luftplasma berichtet.
Die allgemein anerkannte Methode, um mit einem Luftplasma gute Löcher von 37 mm Durchmesser bis hinunter zur Materialstärke mit minimaler Verjüngung zu erhalten, ist:
-
Verwenden Sie den empfohlenen Schneidstrom für Verbrauchsmaterialien.
-
Verwenden Sie die feste (kein THC) empfohlene Schnitthöhe für Verbrauchsmaterialien.
-
Reduzierung von 60 % auf 70 % der empfohlenen Vorschubgeschwindigkeit von Verbrauchsmaterialien und Materialien.
-
Beginnen Sie die Einfahrt in oder nahe der Mitte des Lochs.
-
Senkrechte Zuführung verwenden.
-
Kein Ausbrennen, entweder ein leichtes Überbrennen (engl. over burn) oder frühes Abfackeln (engl. early torch off), je nachdem, was für Sie am besten funktioniert.
Sie müssen experimentieren, um die exakte Lochgröße zu erhalten, da die Schnittfuge (engl. kerf) bei dieser Methode breiter ist als beim üblichen geraden Schnitt."
Diese Verlangsamung kann erreicht werden, indem Sie die Vorschubrate direkt in Ihrem Postprozessor manipulieren oder indem Sie einen adaptiven Vorschub und einen analogen Pin als Eingang verwenden. Auf diese Weise können Sie M67/M68 verwenden, um den Prozentsatz des gewünschten Vorschubs einzustellen, bei dem geschnitten werden soll.
-
Den Vorschubsgeschwindigkeit kennen
Aus der vorangegangenen Diskussion geht hervor, dass der Plasmaregler die vom Benutzer eingestellte Vorschubgeschwindigkeit kennen muss. Dies stellt ein Problem mit LinuxCNC dar, da die Vorschubrate von LinuxCNC nicht gespeichert wird, nachdem der G-Code gepuffert und analysiert wurde. Es gibt zwei Ansätze, um dies zu umgehen:
-
Ordnen Sie den F-Befehl neu zu und speichern Sie die Befehlsvorschubrate im G-Code über einen M67/M68-Befehl.
-
Speichern der Schnittdiagramme in der Plasmasteuerung und Abfrage der aktuellen Vorschubrate durch das G-Code-Programm (wie QtPlasmaC).
Eine neu zu LinuxCNC 2.9 hinzugefügte Funktion, die für das Plasmaschneiden nützlich ist, sind die Status-Tags. Dadurch wird ein „Tag“ hinzugefügt, das der Bewegung zur Verfügung steht und die aktuellen Vorschübe und Geschwindigkeiten für alle aktiven Bewegungsbefehle enthält.
14. I/O-Pins für Plasma-Controller
Plasmaschneider benötigen mehrere zusätzliche Pins. In LinuxCNC gibt es keine festen Regeln darüber, welcher Pin was macht. In dieser Diskussion gehen wir davon aus, dass der Plasmawechselrichter über eine CNC-Schnittstelle verfügt und die Controllerkarte über aktive hohe Eingänge verfügt (z. B. Mesa 7I76E).
Plasmatische können große Maschinen sein und wir empfehlen Ihnen, sich die Zeit zu nehmen, separate Max/Min-Endschalter und Zielsuchschalter für jedes Gelenk zu installieren. Die Ausnahme könnte die untere Grenze der Z-Achse sein. Wenn ein Zielsuchschalter ausgelöst wird, verzögert sich das Gelenk ziemlich langsam für maximale Genauigkeit. Das heißt, wenn Sie Zielsuchgeschwindigkeiten verwenden möchten, die der Tischgröße entsprechen, können Sie den ursprünglichen Auslösepunkt um 50-100 mm überschreiten. Wenn Sie einen gemeinsamen Home-/Endschalter verwenden, müssen Sie den Sensor mit dem letzten HOME_OFFSET vom Auslösepunkt entfernen, oder Sie lösen einen Endschalterfehler aus, wenn die Maschine aus dem Homing kommt. Dies bedeutet, dass Sie 50 mm oder mehr Achsweg mit gemeinsamen Home-/Endschaltern verlieren können. Dies geschieht nicht, wenn separate Haus- und Endschalter verwendet werden.
Die folgenden Pins sind in der Regel erforderlich (beachten Sie, dass vorgeschlagene Verbindungen möglicherweise nicht für eine QtPlasmaC-Konfiguration geeignet sind):
14.1. Lichtbogen (engl. Arc) OK (input)
-
Der Wechselrichter schließt potenzialfreie Kontakte, wenn ein gültiger Lichtbogen hergestellt wird
-
Schließen Sie die Feldspannung an eine ArcOK-Klemme des Wechselrichters an.
-
Schließen Sie andere OK-Klemmen des Wechselrichters an den Eingangspin an.
-
Normalerweise verbunden mit einem der ``motion.digital-``<nn> Pins für die Verwendung von G-Code mit M66
14.2. Brenner an (Ausgang)
-
Löst ein Relais aus, um den Brenner-Einschalter im Inverter zu schließen.
-
Verbinden Sie die Brennerklemmen am Inverter mit den Relaisausgangsklemmen.
-
Verbinden einer Seite der Spule mit dem Ausgangspin.
-
Verbinden Sie die andere Seite der Spule mit der Masse der Feldversorgung.
-
Wenn ein mechanisches Relais verwendet wird, schließen Sie eine Rücklaufdiode (z. B. IN400x-Serie) über die Spulenanschlüsse an, wobei das Band auf der Diode zum Ausgangspin zeigt.
-
Bei Verwendung eines Solid State Relais muss ggf. die Polarität an den Ausgängen beachtet werden.
-
Unter bestimmten Umständen kann das integrierte Spindelrelais auf einer Mesa-Karte anstelle eines externen Relais verwendet werden.
-
Normalerweise mit
spindle.0.on
verbunden.
Warnung
|
Es wird dringend empfohlen, dass der Brenner nicht aktiviert werden kann, während dieser Pin falsch ist, da der Brenner sonst nicht gelöscht wird, wenn der Notaus (engl. estop) gedrückt wird. |
14.3. Gleitender Schalter (engl. float switch) (input)
-
Wird für die Oberflächensondierung verwendet. Ein Sensor oder Schalter, der aktiviert wird, wenn der Brenner nach oben gleitet, wenn er auf das Material trifft.
-
Schließen Sie den Ausgang des Näherungssensors an den ausgewählten Eingangspin an. Wenn mechanische Schalter verwendet werden. Schließen Sie eine Seite des Schalters an die Feldleistung und die andere Seite des Schalters an den Eingang an.
-
Normalerweise mit
motion.probe-input
verbunden.
14.4. Ohmscher Sensor aktivieren (Ausgang)
-
Siehe den Schaltplan ohmic sensing.
-
Verbinden Sie den Ausgangspin mit einer Seite des Trennrelais und die andere Seite mit der Masse der Feldversorgung.
-
In einer Nicht-QtPlasmaC-Konfiguration in der Regel ausgelöst durch einen ``motion.digital-out-``<nn>, so dass er im G-Code von
M62
/M63
/M64
/M65
gesteuert werden kann.
14.5. Ohmsche Sensorik (engl. ohmic sensing) (Eingang)
-
Beachten Sie das zuvor gezeigte Schema zu ohmic sensing.
-
Eine isolierte Stromversorgung löst ein Relais aus, wenn der Brennerschild das Material berührt.
-
Schließen Sie die Feldspannung an eine Ausgangsklemme und die andere an den Eingang an.
-
Achten Sie auf die Polarität der Relais, wenn optoentkoppelte Halbleiterrelais verwendet werden.
-
Üblicherweise an
motion.probe-input
angeschlossen und evtl. mit dem Schwimmerschalter verbunden.
Wie man sieht, sind Plasma-Tische sehr Pin-intensiv, und wir haben bereits etwa 15 Eingänge verbraucht, bevor der normale Notaus-Schalter hinzugefügt wird. Andere haben andere Ansichten, aber der Autor ist der Meinung, dass die Mesa 7I76E der billigeren 7I96 vorzuziehen ist, um MPGs, Skalen- und Achsenwahlschalter und andere Funktionen zu ermöglichen, die Sie vielleicht im Laufe der Zeit hinzufügen möchten. Wenn Ihr Tisch Servos verwendet, gibt es eine Reihe von Alternativen. Es gibt zwar auch andere Anbieter, aber wenn Sie Ihre Maschine um das Mesa-Ökosystem herum konstruieren, wird die Verwendung ihrer THCAD-Platine zum Lesen der Lichtbogenspannung vereinfacht.
14.6. Brenner-Abreißsensor (engl. torch breakaway sensor)
-
Wie bereits erwähnt, sollte ein Abreißsensor installiert werden, der ausgelöst wird, wenn die Brenner irgendwo gegenläuft und herunterfällt.
-
Normalerweise wird dies mit
halui.program-pause
verbunden, damit der Fehler behoben und das Programm fortgesetzt werden kann.
15. G-Code für Plasmasteuerungen
Die meisten Plasmasteuerungen bieten eine Methode zur Änderung von Einstellungen über G-Code. LinuxCNC unterstützt dies über M67
/M68
für analoge Befehle und M62
-M65
für digitale (Ein/Aus-Befehle). Wie dies implementiert wird, ist völlig willkürlich. Schauen wir uns an, wie die LinuxCNC QtPlasmaC Konfiguration dies tut:
M190 Pn M66 P3 L3 Q1 F#<_hal[plasmac.cut-feed-rate]> M3 S1
Anmerkung
|
Benutzer mit einer sehr großen Anzahl von Einträgen in der QtPlasmaC-Materialtabelle müssen möglicherweise den Q-Parameter (z.B. von Q1 auf Q2) erhöhen. |
15.1. Aktivieren/Deaktivieren des THC-Betriebs:
M62 P2 deaktiviert die THC (synchronisiert mit der Bewegung) M63 P2 aktiviert die THC (synchron mit der Bewegung) M64 P2 deaktiviert die THC (sofort) M65 P2 aktiviert THC (sofort)
M67 E3 Q0 würde die Geschwindigkeit auf 100% der angeforderten~Geschwindigkeit setzen M67 E3 Q40 würde die Geschwindigkeit auf 40% der angeforderten~Geschwindigkeit setzen M67 E3 Q60 würde die Geschwindigkeit auf 60% der angeforderten~Geschwindigkeit setzen M67 E3 Q100 würde die Geschwindigkeit auf 100% der angeforderten~Geschwindigkeit setzen
G41.1 D#<_hal[plasmac_run.kerf-width-f]> ; für links von der programmierten Bahn G42.1 D#<_hal[plasmac_run.kerf-width-f]> für rechts von der programmierten Bahn G40 zum Ausschalten der Kompensation
Anmerkung
|
Integratoren sollten sich mit der LinuxCNC-Dokumentation für die verschiedenen oben erwähnten LinuxCNC-G-Code-Befehle vertraut machen. |
16. Externe Offsets und Plasmaschneiden
Externe Offsets wurden in LinuxCNC mit Version 2.8 eingeführt. Durch externe, bedeutet es, dass wir einen Offset außerhalb des G-Codes, dass die Flugbahn Planer weiß nichts über anwenden können. Es ist am einfachsten, mit einem Beispiel zu erklären. Stellen Sie sich eine Drehmaschine mit einem externen Offset vor, der durch eine mathematische Formel angewendet wird, um eine Nocke auf einer Kurve zu bearbeiten. Die Drehmaschine dreht sich also blind herum, wobei der Schnittdurchmesser auf einen festen Durchmesser eingestellt ist, und die externe Verschiebung bewegt das Werkzeug nach innen und außen, um die Nocke über eine angewandte externe Verschiebung zu bearbeiten. Um unsere Drehmaschine so zu konfigurieren, dass sie diese Nocke bearbeitet, müssen wir einen Teil der Achsengeschwindigkeit und -beschleunigung den externen Offsets zuweisen, sonst kann sich das Werkzeug nicht bewegen. An dieser Stelle kommt die INI-Variable OFFSET_AV_RATIO ins Spiel. Angenommen, wir entscheiden, dass wir 20 % der Geschwindigkeit und Beschleunigung dem externen Offset der Z-Achse zuweisen müssen. Wir setzen diesen Wert auf 0,2. Dies hat zur Folge, dass die maximale Geschwindigkeit und Beschleunigung für die Z-Achse der Drehmaschine nur 80 % des möglichen Wertes beträgt.
Externe Offsets sind eine sehr leistungsfähige Methode, um die Brennerhöhe über ein THC an der Z-Achse anzupassen. Aber beim Plasma dreht sich alles um hohe Geschwindigkeiten und schnelle Beschleunigungen, so dass es keinen Sinn macht, diese Parameter zu begrenzen. Glücklicherweise wird in einer Plasmamaschine die Z-Achse entweder zu 100% vom THC kontrolliert oder nicht. Während der Entwicklung der externen Offsets von LinuxCNC wurde erkannt, dass sich die Bewegung der Z-Achse durch G-Code und THC gegenseitig ausschließt. Dies ermöglicht es uns, externe Offsets so auszutricksen, dass sie jederzeit 100 % der Geschwindigkeit und Beschleunigung ergeben. Wir können dies tun, indem wir die Geschwindigkeits- und Beschleunigungseinstellungen der Z-Achse der Maschine in der INI-Datei verdoppeln und OFFSET_AV_RATIO = 0,5 einstellen. Auf diese Weise stehen 100% der maximalen Geschwindigkeit und Beschleunigung sowohl für Sondierung als auch für THC zur Verfügung.
Beispiel: An einer metrischen Maschine mit einem NEMA23-Motor mit Direktantrieb auf einen 5 mm-Kugelgewindetrieb wurden 60 mm/s Maximalgeschwindigkeit und 700 mm/s2 Beschleunigung als sichere Werte ohne Schrittverlust ermittelt. Stellen Sie für diese Maschine die Z-Achse in der INI-Datei wie folgt ein:
[AXIS_Z] OFFSET_AV_RATIO = 0.5 MAX_VELOCITY = 120 MAX_ACCELERATION = 1400
Für das mit dieser Achse verbundene Gelenk würden die Geschwindigkeits- und Beschleunigungsvariablen wie folgt festgelegt:
[JOINT_n] MAX_VELOCITY = 60 MAX_ACCELERATION = 700
Für weitere Informationen über externe Offsets (für Version 2.8 oder später) lesen Sie bitte die [AXIS_<letter>] Abschnitt der Beschreibung der INI-Datei und Externe Achsen Offsets in der LinuxCNC Dokumentation.
17. Messen der Lichtbogenspannung (engl. arc voltage) mit dem Mesa THCAD
Das Mesa THCAD-Board ist ein bemerkenswert preisgünstiger und präziser Spannungs-Frequenz-Wandler, der für die feindliche, laute elektrische Umgebung im Zusammenhang mit Plasmaschneiden ausgelegt ist. Intern hat es einen Bereich von 0-10 V. Dieser Bereich kann einfach durch Hinzufügen einiger Widerstände erweitert werden, wie in der Dokumentation beschrieben. Dieses Board ist in drei Versionen erhältlich, das neuere THCAD-5 mit einem Bereich von 0–5 V, das THCAD-10 mit einem Bereich von 0–10 Volt und das THCAD-300, das für einen erweiterten Bereich von 300 Volt vorkalibriert ist. Jede Platine wird einzeln kalibriert und auf der Platine ist ein Aufkleber angebracht, der die Frequenz bei 0 Volt und Vollausschlag angibt. Für die Verwendung mit LinuxCNC wird empfohlen, den 1/32-Teiler über den entsprechenden Link auf der Platine auszuwählen. Stellen Sie in diesem Fall sicher, dass Sie die angegebenen Frequenzen auch durch 32 teilen. Dies ist besser für den 1 kHz-Servo-Thread geeignet und lässt dem THCAD auch mehr Zeit, um die Ausgabe zu mitteln und zu glätten.
Es gibt eine Menge Verwirrung darüber, wie die THCAD-Ausgabe zu dekodieren ist. Betrachten wir also das Mesa 7I76E und das THCAD-10 für einen Moment mit den folgenden hypothetischen Kalibrierungsdaten:
-
Skalenendwert ≙ 928 kHz (928 kHz/32 = 29 kHz)
-
0 V ≙ 121,6 kHz (121,6 kHz/32 = 3,8 kHz)
Da der Skalenendwert 10 Volt beträgt, ist die Frequenz pro Volt:
(29000 Hz - 3800 Hz) / 10 V = 2520 Hz per Volt
Angenommen, wir haben einen 5 Volt Eingang, so wäre die berechnete Frequenz:
(2520 Hz/V * 5 V) + 3800 Hz = 16400 Hz
Jetzt sollte klar sein, wie man die Frequenz in die entsprechende Spannung umwandelt:
Spannung = (Frequenz [Hz] - 3800 Hz) / (2520 Hz/V)
17.1. THCAD Verbindungen
Auf der Hochspannungsseite:
-
Verbinden Sie die geteilte oder rohe Lichtbogenspannung mit IN+ und IN-
-
Verbinden Sie die Abschirmung des Verbindungskabels mit dem Schirmanschluss.
-
Verbinden Sie die andere Abschirmungsklemme mit der Rahmenmasse.
Angenommen, er ist an ein Mesa 7I76E angeschlossen, verbinden Sie den Ausgang mit dem Spindelgebereingang:
-
THCAD +5 V an TB3 Pin 6 (+5 VP)
-
THCAD -5 V an TB3 Pin 1 (GND)
-
THCAD FOUT+ an TB3 Pin 7 (ENC A+)
-
THCAD FOUT- an TB3 Pin 8 (ENC A-)
17.2. THCAD-Erstprüfung
Vergewissern Sie sich, dass Sie die folgenden Zeilen in Ihrer INI-Datei haben (vorausgesetzt, Sie haben eine Mesa 7I76E):
setp hm2_7i76e.0.encoder.00.scale -1 setp hm2_7i76e.0.encoder.00.counter-mode 1
Schalten Sie Ihren Controller ein und öffnen Sie Halshow (AXIS: Show Homing Configuration), suchen Sie den hm2_7i76e.0.encoder.00.velocity pin
. Bei angelegten 0 Volt sollte er um die 0-Volt-Frequenz (3.800 in unserem Beispiel) schwanken. Nehmen Sie eine 9-Volt-Batterie und schließen Sie sie an IN+ und IN- an. Für ein THCAD-10 können Sie nun die erwartete Geschwindigkeit berechnen (26.480 in unserem hypothetischen Beispiel). Wenn Sie diesen Test bestehen, dann sind Sie bereit, Ihre LinuxCNC Plasmasteuerung zu konfigurieren.
17.3. Welches THCAD-Modell soll verwendet werden?
Der THCAD-5 ist nützlich, wenn Sie beabsichtigen, ihn für die Ohmsche Messung zu verwenden. Zweifellos ist das THCAD-10 das flexiblere Gerät und die Skalierung lässt sich leicht ändern. Es gibt jedoch eine Einschränkung, die bei einigen billigeren Plasmaschneidern mit eingebautem Spannungsteiler ins Spiel kommen kann. Das heißt, die internen Widerstände können vom THCAD als Teil seines eigenen externen Widerstands erfasst werden und fehlerhafte Ergebnisse liefern. Zum Beispiel muss der 16:1-Teiler auf den Plasmaschneidern von Everlast als 24:1 behandelt werden (und 50:1 wird 75:1). Bei namhafteren Marken (z. B. Thermal Dynamics, Hypertherm, ESAB usw.) ist dies kein Problem. Wenn Sie also niedrigere Schneidspannungen als erwartet sehen, ist es möglicherweise vorzuziehen, den THCAD neu zu konfigurieren, um die rohe Lichtbogenspannung zu lesen.
Da Plasmalichtbogenspannungen potenziell tödlich sind, werden hier einige Kriterien vorgeschlagen.
Da keine nennenswerten elektromagnetischen Störungen zu erwarten sind, können Sie den THCAD sicher in Ihrem Schaltschrank installieren, wenn Sie unsere Konstruktionsrichtlinien befolgen.
-
Wenn Sie keinen Spannungsteiler haben, installieren Sie entweder Skalierungswiderstände im Plasmaschneider und installieren Sie den THCAD im Bedienfeld oder folgen Sie den Vorschlägen für HF-Startmaschinen.
-
Wenn Sie einen Spannungsteiler haben, installieren Sie einen THCAD-10 in Ihrem Schaltschrank. Wir hatten keine Probleme mit dieser Konfiguration bei einem 120-A-Plasmaschneider von Thermal Dynamics.
Installieren Sie den THCAD am Wechselrichter, da das Frequenzsignal weitaus unempfindlicher gegenüber EMI-Rauschen ist.
-
Wenn Sie keinen Spannungsteiler haben und im Plasmaschneider Platz haben, installieren Sie ein THCAD-300 im Plasmaschneider.
-
Wenn Sie keinen Spannungsteiler haben und innerhalb des Plasmaschneidgeräts keinen Platz haben, installieren Sie ein THCAD-10 in einem Metallgehäuse außerhalb des Plasmaschneidgeräts und installieren Sie jeweils 50% des Skalierungswiderstands an IN+ und IN- innerhalb des Plasmaschneidgeräts, damit keine tödlichen Spannungen aus dem Gehäuse kommen.
-
Wenn Sie einen Spannungsteiler haben, installieren Sie einen THCAD-10 in einem Metallgehäuse außerhalb des Plasmaschneiders.
In diesem Fall sind unabhängig von der Lichtbogenstartmethode wahrscheinlich bereits Widerstände in der Schaltung enthalten, um tödliche Schocks zu vermeiden, daher wird ein THCAD-10 empfohlen, damit dieser Widerstand (normalerweise 200 kΩ) bei der Auswahl eines solchen Skalierungswiderstands berücksichtigt werden kann Widerstände verzerren die vom THCAD-300 gemeldete Spannung.
18. Postprozessoren und Verschachtelung
Plasma unterscheidet sich insofern nicht von anderen CNC-Bearbeitungen, als es sich um eine solche handelt:
-
In CAD entworfen (wo es als DXF- oder manchmal SVG-Format ausgegeben wird).
-
Verarbeitet in CAM, um den endgültigen G-Code zu erzeugen, der in die Maschine geladen wird
-
Schneiden der Teile über CNC-G-Code-Befehle.
Einige Leute erzielen gute Ergebnisse mit Inkscape und G-Code-Tools, aber SheetCam ist eine sehr preisgünstige Lösung und es gibt eine Reihe von Postprozessoren für LinuxCNC. SheetCam verfügt über eine Reihe von erweiterten Funktionen für das Plasmaschneiden und für den Preis ist es ein Kinderspiel für jeden, der regelmäßig plasmaschneidet.
19. Design für Umgebungen mit Elektrosmog
Plasmaschneiden ist von Natur aus eine extrem feindliche und laute elektrische Umgebung. Wenn Sie EMI-Probleme haben, werden die Dinge nicht richtig funktionieren. Ein offensichtliches Beispiel ist, dass der Brenner gezündet wird und der Computer neu startet, aber es kann auch eine Reihe anderer seltsamer Symptome geben. Sie treten fast alle nur auf, wenn der Brenner schneidet - oft beim ersten Zünden.
Daher sollten Systementwickler die Komponenten sorgfältig auswählen und von Grund auf so konzipieren, dass sie mit dieser feindlichen Umgebung zurechtkommen, um die Auswirkungen elektromagnetischer Störungen (EMI) zu vermeiden. Wird dies nicht beachtet, kann dies zu unzähligen Stunden vergeblicher Fehlersuche führen.
Die Wahl von Ethernet-Karten wie der Mesa 7I76E oder der preiswerteren 7I96 ist hilfreich, da sie es ermöglichen, den PC von der Elektronik und der Plasmamaschine entfernt aufzustellen. Diese Hardware ermöglicht auch die Verwendung von 24-Volt-Logiksystemen, die wesentlich störungsresistenter sind. Die Komponenten sollten in einem Metallgehäuse montiert werden, das mit der Netzerde verbunden ist. Es wird dringend empfohlen, einen EMI-Filter am Netzanschluss zu installieren. Am einfachsten ist es, einen EMI-gefilterten IEC-Netzanschluss zu verwenden, der üblicherweise bei PCs und Elektrogeräten verwendet wird und dies ohne zusätzlichen Aufwand ermöglicht. Planen Sie die Anordnung der Komponenten im Gehäuse so, dass Netzstrom, Hochspannungsmotorleitungen und Logiksignale so weit wie möglich voneinander getrennt sind. Wenn sie sich kreuzen müssen, halten Sie sie in einem Winkel von 90 Grad.
Peter Wallace von Mesa Electronics schlägt vor: "Wenn Sie eine CNC-kompatible Plasmaquelle mit einem Spannungsteiler haben, würde ich den THCAD innerhalb Ihres Elektronikgehäuses zusammen mit der gesamten anderen Bewegungshardware montieren. Wenn Sie eine manuelle Plasmaquelle haben und die Rohspannung des Plasmas ablesen, würde ich den THCAD so nah wie möglich an der Plasmaquelle montieren (sogar im Gehäuse der Plasmaquelle, wenn es passt). Wenn Sie ein abgeschirmtes Gehäuse für die THCAD verwenden, sollte die Abschirmung mit der Masse des Elektronikgehäuses verbunden sein, nicht mit der Masse der Plasmaquelle."
Es wird empfohlen, ein separates Erdungskabel von den Motorgehäusen und dem Brenner zurück zu einem zentralen Sternpunkt an der Maschine zu führen. Verbinden Sie das Plasmaerdungskabel mit diesem Punkt und optional mit einem Erdungsstab, der so nah wie möglich an der Maschine in den Boden getrieben wird (insbesondere bei einer HF-Start-Plasmamaschine).
Die externe Verdrahtung der Motoren sollte abgeschirmt und für den durch den Stromkreis fließenden Strom ausreichend dimensioniert sein. Die Abschirmung sollte auf der Motorseite unverbunden bleiben und auf der Seite des Schaltkastens geerdet werden. Erwägen Sie die Verwendung eines zusätzlichen Pins an allen Anschlüssen des Schaltkastens, so dass die Erdung durch den Schaltkasten hindurch und direkt an der Schritt-/Servomotorsteuerung selbst mit dem Gehäuse geerdet werden kann.
Uns ist mindestens ein kommerzieller Systembauer bekannt, der Probleme mit induziertem elektrischem Rauschen im ohmschen Messkreis hatte. Dies kann zwar durch die Verwendung von Ferritperlen und das Aufwickeln des Kabels gemildert werden, aber es wird auch empfohlen, an der Stelle, an der das ohmsche Messsignal in das Elektronikgehäuse eintritt, einen Netzfilter einzusetzen.
Tommy Berisha, der Meister im Bau von Plasmageräten mit kleinem Budget, sagt: "Wenn Sie ein kleines Budget haben, sollten Sie alte Laptop-Netzteile verwenden. Sie sind sehr gut, filtern gut, sind komplett isoliert, strombegrenzt (das wird sehr wichtig, wenn etwas schief geht), und es ist einfach, 2 oder 3 von ihnen in Reihe zu schalten, da sie isoliert sind. Beachten Sie, dass bei einigen die Erdung mit dem negativen Ausgangskontakt verbunden ist, sie muss also abgeklemmt werden, was einfach durch die Verwendung eines Stromkabels ohne Erdungskontakte möglich ist)."
20. Wasser-Tische
Der minimale Wasserstand unter der Schnittebene des Brenners sollte etwa 40 mm betragen. Es ist gut, wenn unter den Lamellen Platz ist, damit das Wasser während des Schneidens ablaufen und entweichen kann; ein wenig Wasser über der zu schneidenden Metallplatte ist wirklich gut, da es das bisschen Staub beseitigt. Die Zugabe von Backpulver zum Wasser hält den Tisch für viele Jahre in einem guten Zustand, da es keine Korrosion zulässt, während die Lamellen unter Wasser sind, und es reduziert auch den Geruch des Wasserdampfes. Manche Leute verwenden ein Wasserreservoir mit einem Drucklufteinlass, um das Wasser aus dem Reservoir bei Bedarf auf den Wassertisch zu drücken und so Änderungen des Wasserstands zu ermöglichen.
21. Downdraft-Tische
Viele handelsübliche Tische sind nach unten gezogen, d. h., es werden Ventilatoren eingesetzt, welche die Luft durch die Lamellen nach unten saugen, um Dämpfe und Funken aufzufangen. Oft sind die Tische in Zonen eingeteilt, so dass nur ein Abschnitt unterhalb des Brenners für die Abluft geöffnet ist, wobei häufig Luftkolben und Luftmagnetventile zum Öffnen der Klappen verwendet werden. Das Auslösen dieser Zonen ist relativ einfach, wenn Sie die Achsen- oder Gelenkposition von einem der Bewegungspins und die Lincurve-Komponente verwenden, um die Abluftzonen dem richtigen Ausgangspin zuzuordnen.
22. Design für Geschwindigkeit und Beschleunigung
Beim Plasmaschneiden kommt es auf Geschwindigkeit und Beschleunigung an. Je höher die Beschleunigung, desto weniger muss die Maschine bei Kurvenfahrten abbremsen. Das bedeutet, dass das Portal so leicht wie möglich sein sollte, ohne dabei an Torsionssteifigkeit einzubüßen. Ein 100 mm x 100 mm x 2 mm großes Aluminium-Kastenprofil hat die gleiche Torsionssteifigkeit wie ein 80 mm x 80 mm großes T-Nut-Strangpressprofil, ist aber 62 % leichter. Überwiegen also die Vorteile der T-Nuten die zusätzlichen Konstruktionskosten?
23. Zurückgelegte Strecke pro Motorumdrehung
Schrittmotoren leiden unter Resonanz und ein direkt angetriebenes Ritzel bedeutet wahrscheinlich, dass der Motor unter ungünstigen Bedingungen arbeitet. Für Plasmamaschinen wird ein Abstand von etwa 15-25 mm pro Motorumdrehung als ideal angesehen, aber auch etwa 30 mm pro Umdrehung sind noch akzeptabel. Eine Kugelumlaufspindel mit 5 mm Steigung und einer Untersetzung von 3:1 oder 5:1 ist ideal für die Z-Achse.
24. QtPlasmaC LinuxCNC Plasma Konfiguration
Der Link:./qtplasmac.html[QtPlasmaC], der aus einer HAL-Komponente (plasmac.hal) und einer vollständigen Konfiguration für die QtPlasmaC-GUI besteht, hat beträchtlichen Input von vielen in der LinuxCNC-Open-Source-Bewegung erhalten, die das Verständnis von Plasma vorangetrieben haben Controller seit etwa 2015. Es gab viel Test- und Entwicklungsarbeit, um QtPlasmaC in seinen aktuellen Betriebszustand zu bringen. Alles vom Schaltungsdesign bis zur G-Code-Steuerung und Konfiguration ist enthalten. Darüber hinaus unterstützt QtPlasmaC externe THCs wie den Proma 150, kommt aber wirklich zur Geltung, wenn er mit einem Mesa-Controller gekoppelt wird, da dies dem Integrator ermöglicht, den Mesa THCAD-Spannungs-Frequenz-Wandler einzubeziehen, der speziell für die feindliche Plasmaumgebung entwickelt wurde.
QtPlasmaC ist als eigenständig konzipiert und bietet die Möglichkeit, Ihre Schnittdiagramme einzubeziehen, enthält aber auch Funktionen, die mit einem Postprozessor wie SheetCam verwendet werden können.
Das QtPlasmaC-System ist jetzt in Version 2.9 und höher von LinuxCNC enthalten. Es ist jetzt ziemlich ausgereift und wurde seit der ersten Version dieses Handbuchs erheblich verbessert. QtPlasmaC wird die Plasmaunterstützung von LinuxCNC für viele Jahre definieren, da es alle Funktionen eines proprietären High-End-Plasmasteuerungssystems zu einem Open-Source-Preis enthält.
25. Hypertherm RS485 Steuerung
Einige Hypertherm-Plasmaschneider haben eine RS485-Schnittstelle, um der Steuerung (z. B. LinuxCNC) zu ermöglichen, Ampere, Druck und Modus einstellen zu können. Einige Leute haben eine in Python geschriebene Nicht-Echtzeit-Komponente verwendet, um dies zu erreichen. Seit kurzem unterstützt QtPlasmaC diese Schnittstelle nun auch nativ. Lesen Sie in der QtPlasmaC-Dokumentation nach, wie Sie es verwenden können.
Die Kombination aus einer langsamen Baudrate, die von Hypertherm verwendet wird, und der Nicht-Echtzeit-Komponente führt dazu, dass sich der Maschinenzustand nur sehr langsam ändert, so dass es im Allgemeinen nicht möglich ist, Einstellungen während des Schneidens zu ändern.
Bei der Auswahl einer RS485-Schnittstelle auf der PC-Seite haben Benutzer berichtet, dass USB-zu-RS485-Schnittstellen nicht zuverlässig sind. Gute und zuverlässige Ergebnisse wurden mit einer hardwarebasierten RS232-Schnittstelle (z. B. PCI/PCIe oder Motherboard-Port) und einem geeigneten RS485-Konverter erzielt. Einige Benutzer haben über Erfolge mit einer Sunix P/N: SER5037A PCI RS2322-Karte und einem generischen XC4136 RS232-zu-RS485-Konverter (der manchmal auch ein USB-Kabel enthält) berichtet.
26. Postprozessoren für das Plasmaschneiden
CAM-Programme (Computer Aided Manufacture) sind die Brücke zwischen CAD (Computer Aided Design) und der endgültigen CNC-Bearbeitung (Computer Numerical Control). Sie enthalten oft einen vom Benutzer konfigurierbaren Postprozessor, um den Code zu definieren, der für eine bestimmte Maschine oder einen bestimmten Dialekt des G-Codes erzeugt wird.
Viele LinuxCNC-Benutzer sind vollkommen zufrieden mit der Verwendung von Inkscape zu konvertieren SVG vektorbasierten Dateien in G-Code. Wenn Sie mit einem Plasmaschneider für Hobby-oder Heimgebrauch sind, sollten Sie diese Option.
Wenn Ihre Anforderungen jedoch komplexer sind, ist die wahrscheinlich beste und preiswerteste Lösung SheetCam. SheetCam unterstützt sowohl Windows als auch Linux und es sind Postprozessoren dafür verfügbar, einschließlich der QtPlasmaC-Konfiguration. SheetCam ermöglicht das Verschachteln von Teilen über eine ganze Materialplatte und erlaubt die Konfiguration von Toolsets und Codeschnipseln nach Ihren Bedürfnissen. SheetCam-Postprozessoren sind Textdateien, die in der Programmiersprache Lua geschrieben sind und im Allgemeinen leicht an Ihre genauen Anforderungen angepasst werden können. Weitere Informationen finden Sie auf der SheetCam-Website und in deren Support-Forum.
Ein weiterer beliebter Postprozessor ist in dem beliebten Fusion360-Paket enthalten, aber die enthaltenen Postprozessoren müssen angepasst werden.
LinuxCNC ist eine CNC-Anwendung und Diskussionen über andere CAM-Techniken als diese Einführungsdiskussion liegen außerhalb des Rahmens von LinuxCNC.